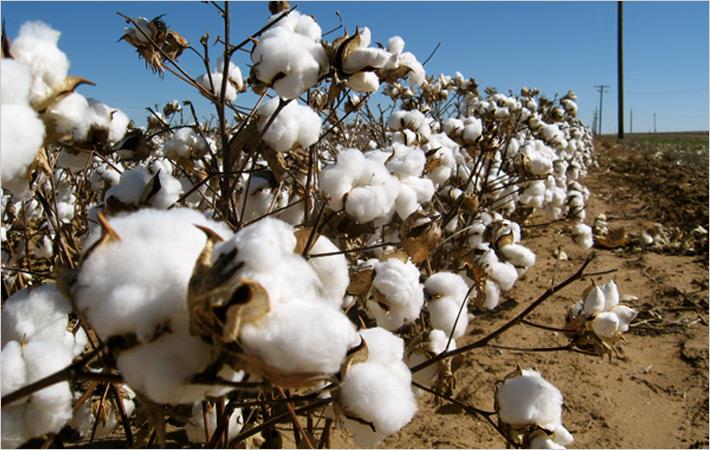
Source: fibre2fashion
he textile mill segment now understands that by logical running a plant and by feeling the positive cross-ventilation effect in conditioned premises, they can comfort-process parameters to achieve around 10 per cent more productivity, says Ashok Senthuraman.
The textile mill now has increased production and production-related automation; so, heat rejection by machines is more and machines have less space in between to exhaust out hotter air. But they still run their old AC plants with obsolete practices without monitoring.
The industry has understood that the distribution losses to be reduced start from the poor functioning of nozzles as well as the pumping losses and simultaneously can improve the humidification effect immensely. Apart from the time-based preventive maintenance schedules for a humidification plant, its condition-based monitoring helps in total productive maintenance (TPM) in a practical way.
Existing operating conditions and symptoms
Kindly go through the following conditions of an AC plant and please try to match to the existing plant that has similar symptoms of working. If so, many of the symptoms can be corrected at no greater extra cost; one can visualise shortly that the humidification plant improves the productivity. These finer symptoms show how a mill treats its AC plant and the effects seen practically.
1. The plant is partly used, like switch off fans and pump for sake of power saving;
2. Water is hard, higher TDS (total dissolved solids), and sedimentation is more in pipes inside and outside;
3. Fans have fluff scaling at hub, blades, densely loaded with dust and fluff;
4. Conditioned premises RH (relative humidity) and temperature not sling-measured across the conditioned area;
5. RH and temperature are sensed at one stagnant spot, giving deviations within the conditioned premises;
6. Water in the sump is very chilled due to choking mist louvers, compared to ambient wet bulb;
7. Water pump discharge pressure is not measured and when measured, it is deviating from normal;
8. Sharp pipe elbows immediately at pump discharge to header and to vertical raiser pipes;
9. Suction and discharge piping mismatched to fluid velocity in pipes;
10. Rusted GI (galvansed iron) piping at the water circuit and need to change over to rigid PVC water pipings;
11. Half of nozzles water jetting, the tail nozzles are plugged, pissing or oozing;
12. Vertical raiser pipes are not tee-linked to each other and to tail end discharge header;
13. Water piping with high-friction head losses, heavily scaled inside and outside;
14. User conserves electricity by not running water pump, fan often and falsely satisfying;
15. Sharp bends instead of contour at supply plenum at masonry, at air ducts;
16. Positive cross-ventilation is not there in premises, but hot pockets existing;
17. Hotspots near equipments, motors are becoming hotter day by day;
18. The user thinks humidification plant is unwanted, but mandatory liability;
The closed loop pump discharge pressure control VFD (variable frequency drive) can be retrofitted to pump circuit to maintain the optimum head and delivery water pressure between 1.5 to 3 Kgsc band to suit to the plant operating conditions. Many mills are using VFD for namesake only and manually setting the Hz to set discharge pressure. The pump can only eject at 10Hz at 20 per cent loading and mills need to optimise setting in the mid range of head band in metres of water column as mentioned in pump nameplate.
Water online metering is a must for a humidification plant. This helps to assess the plantperformance daily. When water circuit gets choked in the spray segment, this is shown in reduced water intake per day and we can take early steps to rectify it. Moreover, whether right amount of water to be mixed with air per hour as stipulated by manufacturer is daily followed or not, can be studied. Less water per hour consumed by plant today compared to yesterday means humidification efficiency is deteriorating day by day for the given load.
The sump water temperature in the spray chamber is the practical day-to-day indicator of Humidification plant efficiency versus Scaling and choking in the spray chamber. This shows the water circuit resistance in the air washer area and its choking status and the need to clean up the air washers. Daily monitoring of sump temperature will indicate plant correct working. The cooler the sump water temperature today compared to yesterday, the more is the choke in the distribution at the spray chamber.
For a humidification plant, water softening plant is the first priority. This is similar to giving cool dry air intake to the compressor instead of hot dried stale air, as this aggravates air compressor problems and losing energy. Frequent water analysis is a must before putting the water to use inside the equipments so that we know the TDS, pH, etc, parameters of incoming water and used water; this will ascertain the scaling effects in the wetted parts of the equipments and pipe lines, etc. Rainwater harvesting done in industry premises definitely helps to improve the condition of existing water to reduce its hardness, etc. Planting trees around the AC plant area and around the building helps to retain the moisture inside the mill.